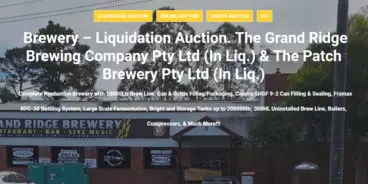
How thermal imaging can save your business from disaster
How thermal imaging can protect your business, by Midland Insurance Brokers.
Key points:
- Thermal imaging can detect any problems areas in the workplace that are susceptible to temperature fluctuations – helping to prevent and manage things like electrical failure or electrical “hot spots”, excessive friction with machinery, moisture penetration or air leaks.
- A thermal scan can reduce the likelihood of problems long before they arise, saving your business from considerable downtime and costly repairs.
- A thermal imaging scan should be conducted every 1 to 3 years (depending on the size and nature of your business).
- Prevention is always better than the cure.
What is thermal imaging and what are its benefits?
Thermal imaging – or thermography – is the process of using a specialised camera to measure infrared radiation emitted by an object regardless of lighting conditions. The varying levels of radiation are then converted into a unique colour gradient that relates to fluctuations in temperature, accurate to one-tenth of a degree.
As a non-invasive and visually concise tool, thermal imaging helps to uncover any potential problem areas in the workplace efficiently and safely. It’s an effective method of protecting your business’ assets, helping to prevent significant loss or damage to stock, equipment, or machinery, and can ensure the safety and security of your employees and your overall operation.
Thermography is used for a variety of purposes, and can return many benefits, like:
- Measuring temperature variations and identifying target areas that need repair
- Reducing outages and electrical energy costs
- Reducing the risk of expensive equipment damage due to electrical fault
- Locating electrical hot spots
- Detecting air leaks and moisture penetration
- Eliminating the need for exploratory demolition
- Minimising long-term repair costs
- Helping to control insurance claims costs
“22% of industrial fires are caused by faulty electrical equipment”
Using thermal imaging to reduce your insurance premiums.
Thermal imaging is becoming increasingly common for many Australian businesses to use as a way to decrease their commercial insurance premiums. Because of the value the technology can provide in preventative maintenance programs, insurance companies are rewarding businesses who are taking action to establish a low-risk environment and fire-reduction strategies. This consequently ends up providing access to lower insurance costs and prevents production downtime.
How often is thermal imaging needed?
There are no set standards – it will depend on the type of equipment your business uses, and the load the system is under.
As a guide, for a regular office building, a thermal imaging scan should be conducted every 2 to 3 years. For a manufacturing site – which has a high-power drain on the electrical systems – a scan at least once a year is advised.
The frequency of a thermal scan for your business can also be more accurately identified during a risk assessment of the premises, or at the request of your insurer or broker.
Below are some of the ‘higher risk’ sectors and environments where an annual thermal imaging scan can help to strengthen a business’s loss prevention program.
Electrical maintenance
Thermal imaging can discover over-heated components in electrical devices and switchboards (preferably while under peak loading), accurately detecting hot spots generated from issues like:
- Loose electrical connections
- Unbalanced loads
- Overloading of electrical circuits
- Deteriorated electrical insulation
- Damage caused by pests chewing on wires
These tests can help prevent serious injury, or even death from electrocution, while also saving your company time and money.
Construction
A thermal scan will help locate building defects such as missing or faulty thermal insulation, heat leaks, delaminating render, and any condensation problems. Results can be used to improve the efficiency of heating and air-conditioning units.
Plumbers
Use thermal imaging to inspect sites of possible leaks, mainly through walls and pipes. Since the devices can be used at a distance, they’re ideal for finding potential problems in equipment that is either hard to reach or might otherwise pose a safety issues to workers.
Cool rooms
Thermal imaging can be used in cool rooms, freezers, and temperature-controlled facilities to identify variances in temperature through vapour leakage or thermal transfer in the insulated panelling. Any fluctuations in temperature can impact product shelf life, not to mention greatly increase energy costs.
A scan is best performed at completion of a cool room construction. It will pinpoint the exact location of a possible thermal leak between panel and connection points.
Roofing
Most roof failures occur within the first seven years. Even if your roof is relatively young, a thermal scan can help reveal any accumulated moisture below the surface – moisture creates an environment conducive to mould.
Infrared inspections can detect issues on roof membranes, saving you the effort and the significant expense of dismantling and replacing the entire surface.
Mechanical equipment and machinery
Thermal imaging can also be used on mechanical equipment to detect issues like motor bearing problems or motor shaft misalignment. When operating under normal load conditions, thermal imaging scans on equipment and machinery can detect:
- Excessive friction
- Non-uniform heat flow
- Temperature distributions
- Motor and bearing wear
- Pipe insulation
- Tank levels
How much does a professional thermal imaging scan cost?
This will depend on the size and nature of your business. Most small commercial buildings can have their main switchboards and associated components inspected for under $500. For larger operations (e.g. a scan of multiple rooms, switchboards or equipment), you can
expect a cost between $1,500 – $2,000.
Even though a good quality thermal camera can be purchased online for around $500 these days, getting a professional to perform an infrared inspection is much more involved than a simple ‘point and shoot’ approach.
A professional inspection is all about gathering accurate and reliable data, having it interpreted correctly, and then clearly communicating those findings to the business owner so that they can make reliable and informed decisions.
Keep in mind that there are regulations for certain industries that require their thermal imaging scan to be completed by someone with a Level 1 Certificate in Infrared Thermography. These industries include: electrical and mechanical, building, horticulture and agriculture, dairy, defence, and security.
Getting a professional thermal imaging scan of your business might seem expensive initially. However, it’s an opportunity to take corrective action so that small issues don’t become big issues – issues that can potentially put you out of business.
Remember, prevention is better than the cure. And a regular scan is a small price to pay for peace of mind.